RFID sensor
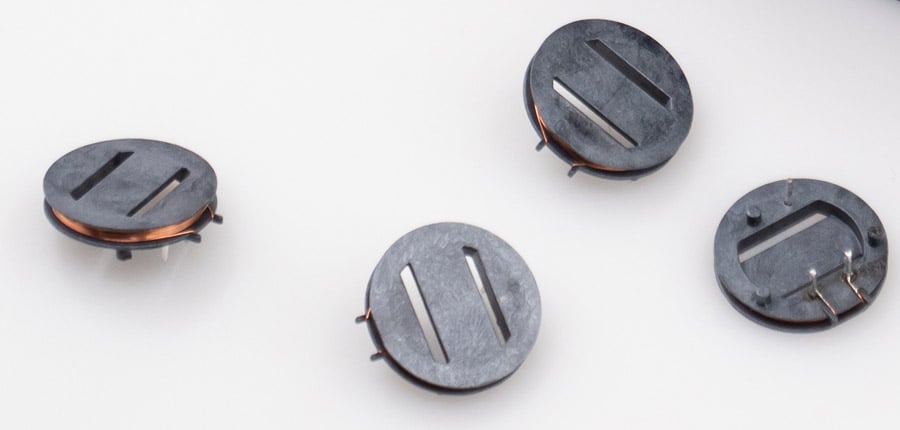
Customer-specific bobbin coil manufactured by KUK Group: At Elesta GmbH, it serves as an antenna in an RFID sensor.
In a larger project, KUK Group supported the Swiss technology company Elesta GmbH in the development of a new generation of functional safety sensors. In addition to the quality of the RFID coil, the optimal support throughout various project phases was convincing.
Elesta took the development of a new generation of RFID sensors as an opportunity to re-qualify suppliers for winding goods. The sensor in question is designed, among other things, for the magnetic monitoring of protective door devices, such as those used for packaging machines. The customer-specific bobbin coil serves as an antenna in this RFID sensor.
The requirements for these safety sensors are very high; for example, their functional safety must be checked every 100 ms under the conditions of machine safety. Compared to the current product, the design has been revised; in addition to technical improvements, the size has also been minimised, making a new RFID coil necessary.
Short response time for prototypes
«For ELESTA GmbH, the most important selection criteria for qualifying suppliers of customer-specific components and engineered parts are technical know-how and support, production of samples, series production and value for money,» says Martin Grimm, system architect at ELESTA GmbH.
KUK Group was outstanding in this project in an early development phase with good support and prototypes.
Modified requirements for bobbin coil implemented
As often happens in demanding technology projects, the client had a number of requirements that changed during the various development phases. "With KUK, we were able to solve all challenges together and at eye level. In addition to the purely technical aspects, the way we worked together was a decisive factor for me," says the experienced developer.
Not only the bobbin coil is customer-specific, but also the packaging. Thanks to the specifically developed tape and reel packaging, the coils at Elesta go directly from incoming goods to SMD production.
Rapid scaling of coil production
The planned series volume is a few 10,000 pieces per year. With its global capacities, KUK is prepared for this. For the time being, the bobbin coil will be manufactured at the production site in Slovakia. From there, they are shipped in batch sizes that are tailored to Elesta's needs.
About Elesta
Elesta GmbH in Bad Ragaz (Switzerland) is part of the Pilz Group, a technology leader in automation engineering. Elesta develops and produces relays with forcibly guided contacts and sensors for functional safety applications. The products are used in a wide range of industries and applications and serve to protect people, processes and the environment.
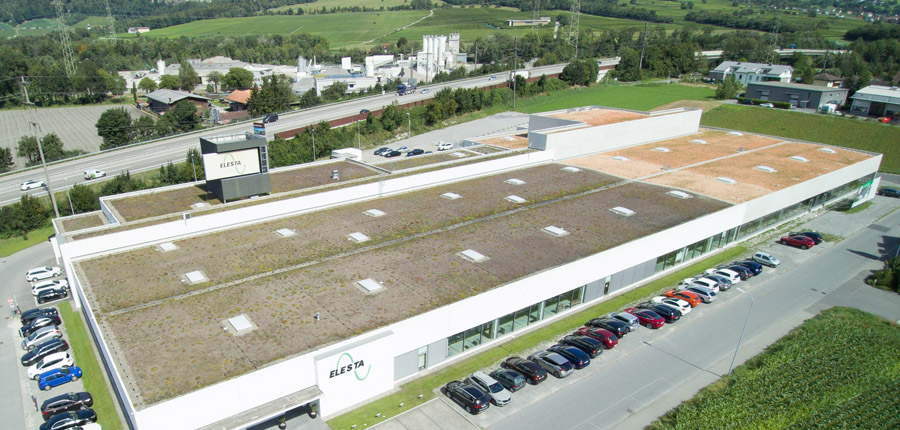
COIL MANUFACTURING AND EMS SERVICES FROM KUK GROUP IN THIS PROJECT
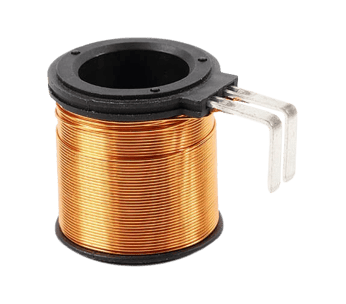
Windings on customer-specific bobbins
KUK offers windings on customer-specific coil formers with all common bobbin shapes and geometries. All conceivable shapes of electric coils are customer-specific manufactured.
NEWS FROM THE PRODUCTION OF COILS AND ELECTRONICS
Insulation layer on magnet wires: A common stumbling block for engineers
What material can coils be wound from?
Self-supported coils: Facts about coils made of selfbonding wire
Misconceptions about the fill factor of electric coils
Myths and facts on edgewise windings
What is the advantage of orthocyclic windings?
READY WITH A NEW PROJECT?
Our experts for coil and electronics manufacturing will be pleased to advise you.